Group-wide Cooperation to Ensure Stable Supply of High-Quality Products
Core Principles
The Otsuka group is committed to providing a stable supply of safe and reliable products that are trusted by all. Furthermore, we aim to obtain appropriate standards certification (ISO 9001 for quality, ISO 22000, and FSSC 22000 for food safety). We promote the cultivation of Quality Culture by advocating a group-wide “Quality Policy.” Furthermore, each operating company formulates its own quality guidelines tailored to its business characteristics. Under the leadership of top management, every individual strives for continuous improvement in product and service quality as a bearer of Otsuka quality.
Promotion System for Pharmaceutical Business
The Otsuka group aims to both improve and maintain product quality guided by international standards in response to requirements in laws and regulations as well as look to improve the functionality of products and ensure a stable supply. For example, Otsuka Pharmaceutical has formulated the policy for pharmaceutical quality assurance, seeking to establish a high-level quality assurance system where all activities in all processes are based on this policy, including those undertaken by external contracted manufacturers. The Pharmaceutical Business established global product quality policy in 2017. Activities are carried out globally, and include ensuring the reliability of quality data and compiling procedural manuals.
Promotion System
The Pharmaceutical Division of the Otsuka group complies with the Act on Securing Quality, Efficacy and Safety of Products including Pharmaceuticals and Medical Devices, and we observe the laws and regulations of the countries where we operate, performing quality control based on Good Quality Practice1 and Good Vigilance Practice2 in manufacturing and sales, and implementing post-marketing safety measures. Moreover, we submit all necessary reports, including those on adverse events, to regulatory authorities, and update and maintain all required documentation (Pharmacovigilance3).
In addition, we ensure that all pharmaceuticals are manufactured under a quality assurance system to enable the stable supply of high-quality products. We have established a quality assurance system that complies with international standards, such as GMP4 in each country and PIC/S5 GMP. We are also strengthening the quality control system based on the ICH Q10 Pharmaceutical Quality System Guidelines.
For instance, in 2023, Otsuka Pharmaceutical obtained a new license for manufacturing and selling medical devices and made changes to our management structure to contribute more to patient care. Also, from the perspective of quality assurance (QA) for products supplied globally, we continue several activities, such as conducting audits of raw material vendors within the group, sharing quality-related information with global subsidiaries, and ensuring a stable supply chain.
- 1:Standards for quality assurance in production and sales (GQP). In Japan, GQP is defined in a ministerial ordinance issued by the Ministry of Health, Labour and Welfare based on the Pharmaceutical and Medical Devices Act. The official name is the Ministerial Ordinance on Standards of Quality Assurance for Drugs, Quasi-drugs, Cosmetics and Medical Devices.
- 2:Standards for post-marketing safety management (GVP). Good post-marketing study practice (GPSP) and GVP are elements of post-marketing surveillance. GVP mandates the establishment of rules for the collection and monitoring of safety information, and the implementation of necessary safety measures after pharmaceuticals and medical devices are launched in the market. In Japan, GVP is defined in a ministerial ordinance issued by the Ministry of Health, Labour and Welfare based on the Pharmaceutical and Medical Devices Act. Its official name is the Ministerial Ordinance on Standards for Post-Marketing Safety Control of Drugs, Quasi-drugs, Cosmetics, Medical Devices, and Regenerative Medicine Products.
- 3:Pharmacovigilance refers to monitoring of drug safety information. It helps to promote appropriate use of drugs and protect patient safety by detecting, evaluating and preventing adverse reactions.
- 4:Standards designed to ensure proper manufacturing control and quality control in all processes from the receiving of raw materials to the shipment of final products. In Japan, GMP is defined in a ministerial ordinance issued by the Ministry of Health, Labour and Welfare based on the Pharmaceutical and Medical Devices Act. Its official name is the Ministerial Ordinance on Standards for Manufacturing Control and Quality Control for Drugs and Quasi-drugs.
- 5:Pharmaceutical Inspection Convention and Pharmaceutical Inspection Co-operation Scheme (PIC/S) is the informal cooperative arrangement between regulatory authorities aimed at the international development, implementation and maintenance of harmonized GMP standards and quality systems for inspecting in the field of medicinal products.
Safety Management
The Otsuka group has established a safety management system that consists of the Quality Assurance Manager, who is responsible for the quality control of pharmaceuticals as required by the Act on Securing Quality, Efficacy and Safety of Products Including Pharmaceuticals and Medical Devices. Under this system, the Safety Control Manager responsible for post-marketing safety management and the General Marketing Compliance Officer oversees compliance. This ensures that actions taken for quality and safety are performed accurately. We also hold monthly debriefings for everyone from the General Marketing Compliance Officer to management.
The Triumvirate Structure in the Manufacture and Sale of Pharmaceuticals
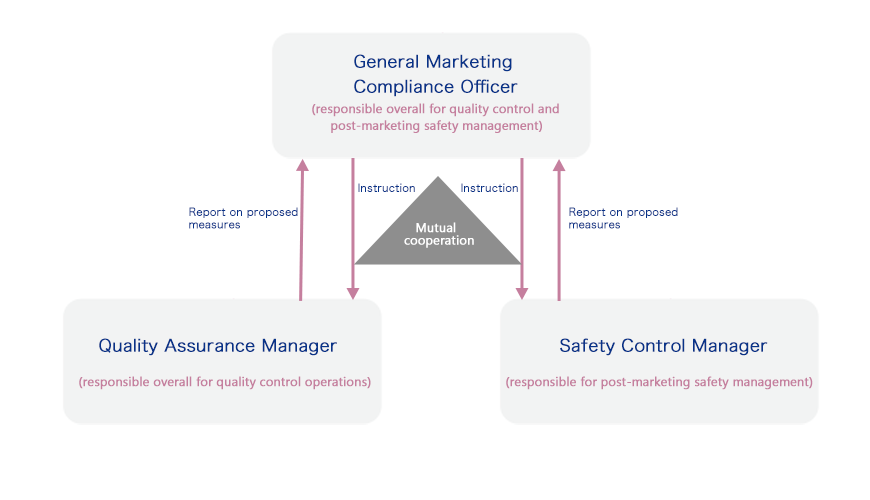
Since 2016, Otsuka Pharmaceutical and group companies have enhanced compliance for a range of processes from development through to the finished product. Monthly debriefings are held with the director in charge of quality in addition to management reviews three times a year. The Nutraceutical Business holds monthly debriefings and quality assurance meetings with the director in charge of quality as part of a thorough quality management system.
Participation in Activities to Raise Awareness of and Eradicate Counterfeit Medicines
In 2021, there were 5,987 reported incidents related to falsified medicines1 and theft worldwide. This represents a 38% increase compared with 2020.2 In addition, in developing countries, where falsified medicines reportedly account for 10–30% of all drugs, patients’ safety is seriously threatened. Otsuka Pharmaceutical participates in raising awareness of and eradicating falsified medicines in collaboration with the Pharmaceutical Security Institute (PSI).3 Otsuka Pharmaceutical and subsidiaries outside of Japan have formed a global product security team that practices market surveillance and cooperation with industry and government so that medicines reach patients through the correct distribution channels. This structure was strengthened in January 2021, and members with expertise from production, quality, procurement, and logistics departments are participating in cross-organizational activities.
- 1:The definition of falsified medicines was discussed at the 2017 WHO World Health Assembly. WHO defined falsified medicines as “medical products that deliberately/fraudulently misrepresent their identity, composition or source.
- 2:Source: The Pharmaceutical Security Institute website
- 3:In 2023, more than forty pharmaceutical companies from around the world fund the Pharmaceutical Security Institute’s (PSI) anti-counterfeit medicine efforts (information gathering, collaboration with law enforcement, and awareness-raising activities).
Global Quality Assurance Officers’ Meeting
Otsuka Pharmaceutical Factory insists on manufacturing IV solutions in the country where they are sold because we believe in supplying pharmaceuticals at fair prices for every country or region so that all people can receive medical treatment equally, whether they are rich or poor. The Otsuka Global Quality Standards have been set to maintain high quality in every country that manufactures our products, aiming to further improve quality. We send young engineers to other countries to oversee production, which also presents a huge opportunity for personal growth for those employees. The Global Quality Assurance Officers’ Meeting is held every year for 15 group companies across 10 countries engaged in the IV solutions business. IV solutions require stricter quality control than other pharmaceuticals, since they are administered directly into the body.
While establishing a framework for exchanging safety data throughout the group, we are working as one to unify our approach to quality assurance and steadily maintain and improve product quality.
Auditing the Quality and Safety of Pharmaceuticals
The Otsuka group regularly conducts internal and external audits on the quality and safety of pharmaceuticals following domestic and international regulations.
For instance, at Otsuka Pharmaceutical within Japan, self-inspections are conducted by the Office of Clinical Quality Assurance once a year based on domestic regulations. The global Quality Assurance Division carries out internal audits based on procedural guidelines. External audits are conducted by regulatory authorities in other countries, as well as by audit departments of pharmaceutical partner companies and external consultants.
See Quality and Safety (Otsuka.co.jp, Japanese language only)
Joint Business Partner Audits by Pharmaceutical Companies
In the Otsuka group, four pharmaceutical companies conduct joint business partner audits for shared suppliers of raw materials. This unique initiative, launched in 2016, is operated with shared systems, such as common auditor training and an auditor certification program.
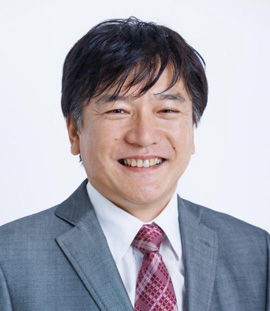
Yasumasa Omote
Director of Quality Assurance Division
Otsuka Pharmaceutical
Joint Business Partner Audits
Through joint efforts by the Otsuka group's pharmaceutical-related companies, we standardized business partner audits and improved the skills of our auditors. This helps us respond to misconduct in the area of quality, which leads to more trusting relationships with raw material suppliers.
Promotion System for the Nutraceutical Business
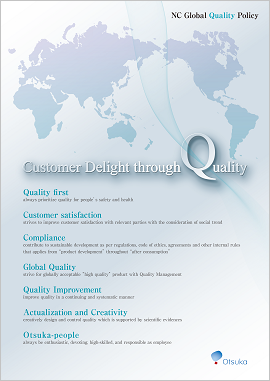
In 2018, Otsuka Pharmaceutical established the Quality Division for making possible quality improvements and safety control for products in the Nutraceutical Business. The Global Product Quality Team consisting of members from 15 Otsuka group companies has begun formulating a common philosophy on quality and the NC Global Quality Policy was established in 2021.
Promotion System
Otsuka Pharmaceutical established a Quality Assurance Office. Based on the concept of good manufacturing practice for pharmaceuticals, the Global Product Quality Team, consisting of members from 15 group companies, built an integrated management system that ranges from identifying and investigating risk to examining the cause of issues that arise and taking effective countermeasures. As an example, in December 2020 Otsuka Pharmaceutical formulated rules for evaluating the quality of nutraceutical products from development to marketing to prevent risks to quality in all aspects of the value chain.
In addition, we are promoting more quality improvements, such as acquiring international certifications at production bases to ensure global quality assurance.
Auditing the Quality and Safety of Nutraceutical Products
In Otsuka Pharmaceutical’s Nutraceutical business segment, factories that have obtained the international food safety certification FSSC 22000 undergo annual maintenance audits as well as recertification audits three times a year from external auditing agencies.
See Quality and Safety (Otsuka.co.jp, Japanese language only)
Listen to the Customer Feedback Meetings
We collect post-marketing information on Otsuka Pharmaceutical’s nutraceutical products. Feedback provided to the Consumer Relations Office is shared with production and technology departments at monthly meetings of the Quality Assurance Office of the Quality Headquarters. The goal is to make and check the progress of product improvements. Listen to the Customer Feedback Meetings have been held every year since 2018, and they have gradually gotten bigger. At these meetings, representatives from purchasing, production, quality, compliance, legal affairs, and Otsuka Holdings share information and work to improve quality from a customer perspective.
Initiatives to Improve Product Quality through Collaboration between Pharmaceutical and Nutraceutical Businesses
In the Group-Wide Global Quality, Production, Supply Chain, and Environment Meeting held in February 2023, we shared quality information with group companies aimed at achieving better quality management. We also recognized and awarded outstanding initiatives, in this way contributing to the development of quality management staff as well as raising awareness.
Human Resource Development and Education System
In addition to regular training on quality for all employees and other stakeholders in accordance with an annual plan, we provide training on topics including: company and manufacturing site rules; safety, health and the environment; and manufacturing management and quality control in relation to products and their manufacture. Depending on the content, human resource development includes practical programs for learning procedures and skills.
For example, Otsuka Pharmaceutical provides education for new recruits, training to improve skills for employees in their second or third year with the company, and training for people to confirm the content of tests, each around 10 times a year. Also, in our Quality Assurance Division, we designed and implemented an exchange program in collaboration with overseas affiliates to foster employees capable of making global contributions as well as to promote mutual understanding of the histories and cultures of other regions through mutual employee exchanges.